The roar of a hot rod engine, the satisfying crunch of the gearshift, and the precise control of the steering wheel – these are the hallmarks of the automotive passion. Now, imagine a hot rod that seamlessly combines this exhilarating experience with the precision and efficiency of electric power steering. This innovative approach promises a dramatic shift in the hot rod community, offering a new frontier in performance, responsiveness, and customization.
Electric power steering systems are quickly becoming a desirable option for high-performance vehicles, including hot rods. They offer significant advantages over traditional hydraulic systems, especially in terms of responsiveness, control, and the ability to tailor the steering feel to individual preferences. The intricate interplay of motors, sensors, and control units allows for precise control and adjustment, unlocking a level of performance previously unimaginable.
Introduction to Electric Steering
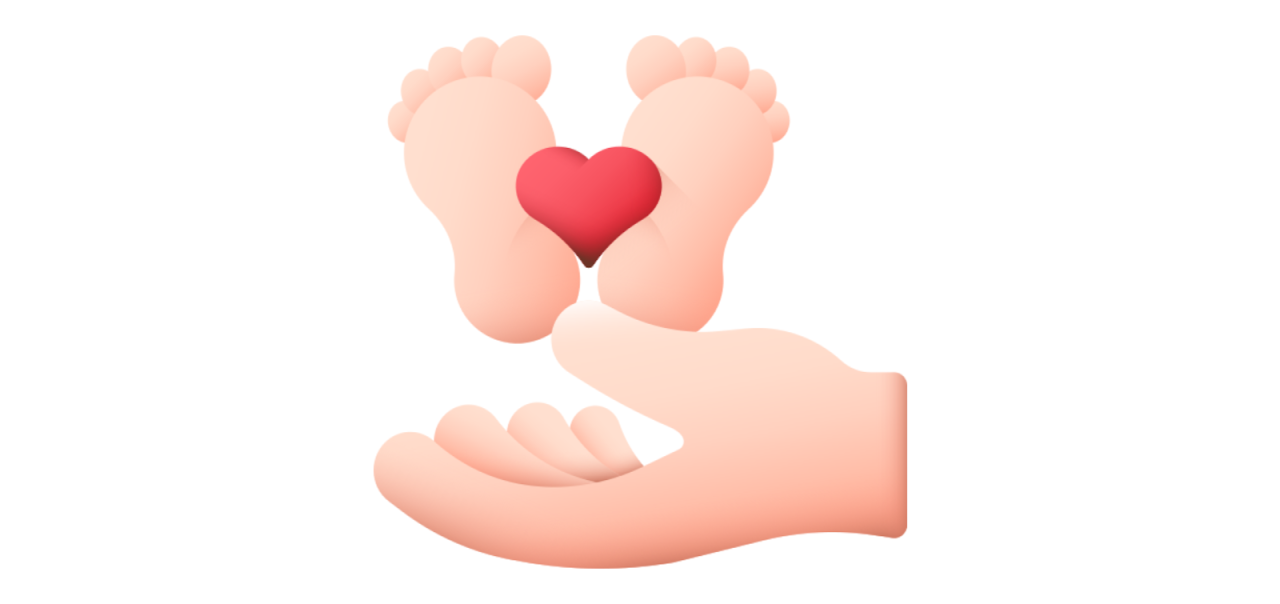
Electric power steering (EPS) systems are rapidly gaining traction in the automotive industry, offering a compelling alternative to traditional hydraulic systems. These systems leverage electric motors and sophisticated control algorithms to provide precise and responsive steering, often with enhanced fuel efficiency and reduced maintenance. The shift towards electric steering is driven by the broader trend toward electrification in the automotive sector, reflecting a push for more sustainable and advanced vehicle technologies.Electric steering systems differ fundamentally from their hydraulic counterparts.
Instead of relying on fluid pressure, EPS systems use electric motors to assist the driver’s steering input. This translates to a different feel and operational characteristics, impacting everything from the initial steering response to the overall driving experience.
Electric vs. Hydraulic Steering Systems
Electric power steering systems offer several key advantages over their hydraulic counterparts. They are generally more efficient, as they don’t require the complex hydraulic pumps and hoses of traditional systems. This translates to improved fuel economy, a crucial factor for vehicles like hot rods that often prioritize performance and customization. The inherent simplicity of electric systems can also lead to reduced maintenance needs.
However, electric systems can sometimes be perceived as lacking the direct, tangible feel of hydraulic systems, although advancements in motor technology and control algorithms are addressing this issue.
Benefits and Drawbacks for Hot Rods
Electric steering offers several advantages for hot rods. The compact size and lighter weight of electric motors are particularly beneficial in customizing the vehicle’s weight distribution, which is essential for performance. Furthermore, the precise control and responsiveness provided by EPS systems can be leveraged to enhance the handling characteristics of a hot rod, optimizing its performance on the track or street.
However, the cost of an EPS system can be a deterrent, especially for hot rod enthusiasts on a tighter budget. The perceived lack of “feel” compared to hydraulic systems may also be a concern for some enthusiasts who value the direct mechanical feedback of hydraulic systems.
Historical Context
The development of electric steering technology has been a gradual process. Early iterations of EPS systems faced challenges in terms of power output and control precision. However, advancements in motor technology and control algorithms have led to significant improvements in performance and efficiency. The rise of electric vehicles has also spurred further innovation in electric steering systems, driving down costs and improving accessibility.
Comparison Table: Electric vs. Hydraulic Steering
Feature | Electric Steering | Hydraulic Steering |
---|---|---|
Responsiveness | Generally very responsive, often with adjustable settings. | Typically responsive, but often with a slightly slower initial response. |
Feel | Can vary depending on the system; some may not match the direct feel of hydraulics. | Generally provides a direct, tangible feel. |
Maintenance | Lower maintenance requirements due to fewer moving parts. | Requires periodic fluid changes and potential pump maintenance. |
Efficiency | Generally more fuel-efficient due to reduced energy consumption. | Generally less fuel-efficient due to hydraulic pump operation. |
Cost | Generally higher initial cost than hydraulic systems. | Typically lower initial cost than electric systems. |
Electric Steering Components for Hot Rods
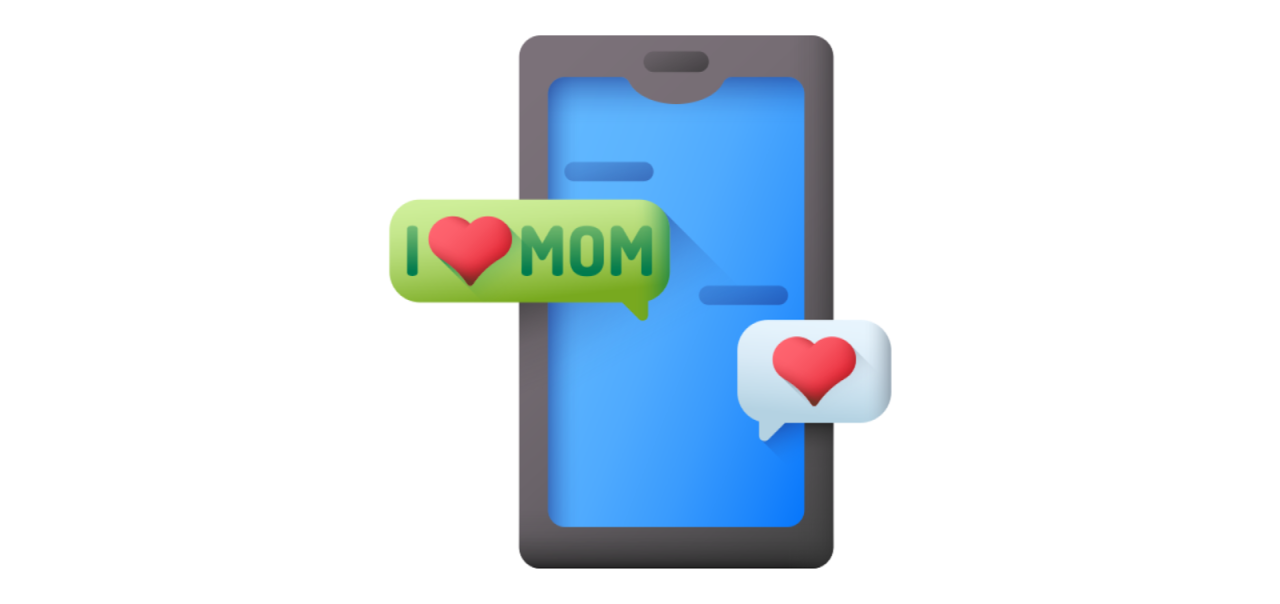
Electric power steering (EPS) is rapidly gaining traction in the hot rod community, offering a compelling blend of performance enhancements and improved driver experience. Beyond the basic concept, the specific components and their interplay within a hot rod application require careful consideration to ensure both efficiency and the handling characteristics desired. The components must withstand the high torque and demanding conditions inherent in these high-performance vehicles.The core components of an electric power steering system, tailored for the unique demands of hot rods, demand robust performance and precision.
Factors like responsiveness, power output, and component durability must be meticulously balanced to maintain the desirable handling characteristics of a hot rod while providing the driver with a precise, responsive feel. Integrating EPS into a hot rod necessitates a thorough understanding of the performance characteristics of the components and their integration into the existing mechanical systems.
Electric Motor Selection
Electric motors are the heart of an EPS system. Their selection is critical for hot rod applications, as they must deliver precise torque and speed control, while withstanding high temperatures and vibration. High-performance motors, typically brushless DC (BLDC) motors, are preferred for their efficiency, power density, and long lifespan. They are also capable of generating a high torque-to-weight ratio, crucial for handling the high-performance demands of hot rods.
Furthermore, their precise control characteristics allow for optimized steering response.
Sensors and Control Units
Sensors play a critical role in providing feedback to the control unit, enabling the system to adjust the motor’s output dynamically. Essential sensors include position sensors (e.g., rotary encoders) that track the steering wheel’s position and speed sensors that monitor the speed of the steering column’s rotation. These sensors ensure the system’s responsiveness and accuracy. The control unit, acting as the “brain” of the system, receives input from the sensors, processes the data, and sends signals to the motor, regulating the steering assistance accordingly.
The control unit’s sophistication directly impacts the system’s precision and responsiveness, impacting the driver’s experience.
Component Specifications
The performance characteristics of the components are paramount in hot rod applications. Motors need to be rated for higher torque and speed than those in standard applications. Similarly, sensors must be capable of withstanding the vibration and stress present in a hot rod’s steering column. The control unit must also be able to handle the processing demands of a high-performance steering system.
High-performance steering systems in hot rods often use higher voltage and current, requiring the use of robust wiring and connectors.
Electric Motor Types
Motor Type | Characteristics | Advantages | Disadvantages |
---|---|---|---|
Brushless DC (BLDC) | High efficiency, high power density, long lifespan, high torque-to-weight ratio | Excellent performance characteristics, precise control, relatively quiet operation | More complex design, potentially higher cost |
Permanent Magnet Synchronous Motors (PMSM) | High efficiency, high power density, smooth operation | Excellent performance, high torque, good efficiency | Potential for higher cost compared to BLDC |
Stepper Motors | Precise position control, good for low-speed applications | Suitable for applications requiring precise positioning of the steering column | Lower power output compared to BLDC or PMSM, might not be ideal for high-performance steering applications |
System Arrangement
The arrangement of components within the hot rod’s steering system is critical for optimal performance and integration. The electric motor is typically mounted directly on the steering column or gearbox. Sensors are strategically placed to capture accurate feedback from the steering column’s movement. The control unit is housed in a protective enclosure, ensuring its safety and stability within the vehicle’s chassis.
Proper routing of wiring is crucial for maintaining electrical integrity and preventing interference. A well-designed layout ensures efficient signal transmission and prevents system failure.
Design Considerations for Electric Steering in Hot Rods
Integrating electric power steering into a hot rod presents unique challenges beyond simply swapping components. The inherent need for a lightweight, compact, and aesthetically pleasing design often conflicts with the demands of robust performance and reliability. This necessitates meticulous consideration of packaging, mounting, and calibration to ensure a seamless and satisfying driving experience.Careful planning and execution are crucial for achieving a harmonious integration of electric steering components within a hot rod’s existing framework.
This involves understanding the chassis’s limitations and strengths to determine the optimal placement and orientation of the electric motor, control unit, and steering gear.
Packaging and Mounting Strategies
Careful consideration of component placement is paramount for optimal performance and aesthetics. The motor, control unit, and steering gear must be packaged efficiently to minimize bulk and maintain a clean, uncluttered look. Different mounting strategies impact steering feel and performance, necessitating a tailored approach for each application.
- Front-mounted configurations typically offer the most compact packaging, but may restrict access for maintenance. This approach is often favored for its aesthetic appeal, particularly in front-engine hot rods.
- Rear-mounted configurations, while less aesthetically intrusive in some cases, can require more complex wiring and routing. They are often preferred when a specific aesthetic or chassis constraint necessitates the relocation of components.
- Under-chassis mounting is an option for a more concealed setup. However, it necessitates careful routing of wiring and the potential for interference with other components. Careful attention to heat dissipation is crucial in this configuration.
Wiring and Electrical Considerations
The electrical system’s complexity increases with the integration of electric steering. Proper wiring, grounding, and insulation are critical to prevent electrical interference and ensure system reliability. Specific consideration must be given to the high-current demands of the electric motor.
- Wiring harnesses should be designed for durability and weather resistance, ensuring longevity in the demanding environment of a hot rod. High-quality connectors are essential to maintain electrical integrity.
- Grounding must be robust and well-distributed to minimize voltage drops and prevent electrical noise. Improper grounding can lead to unpredictable steering behavior and potential component failure.
- Electrical protection devices, such as fuses and circuit breakers, are crucial for safeguarding the system from overloads and short circuits, which are particularly important in high-performance applications. Consider the potential for extreme temperatures and vibrations.
Calibration and Tuning
Precise calibration and tuning are vital for optimizing steering response and feel. This involves adjusting parameters such as motor torque, steering ratio, and feedback mechanisms.
- Steering ratio adjustments impact the amount of driver input required to achieve a specific turn. An ideal ratio balances responsiveness with the feel of a traditional mechanical steering system.
- Calibration involves adjusting the electric motor’s output and the control unit’s feedback to align the steering response with the driver’s expectations. This often requires extensive testing and iterative adjustments.
- Feedback mechanisms are critical to ensure the driver receives accurate and timely information about the steering wheel’s position and the vehicle’s response. This ensures the driver can anticipate the vehicle’s reaction to inputs.
Example: Integrating Electric Steering into a 1932 Ford Roadster
Integrating electric power steering into a 1932 Ford Roadster necessitates a compact front-mounted configuration. The existing chassis provides a challenge in terms of space for components. Careful routing of wiring and the use of high-quality electrical connectors will be critical for reliability. Precise calibration will be necessary to match the Roadster’s intended driving characteristics. This includes balancing steering responsiveness with a light, responsive feel, without compromising the inherent handling characteristics of the hot rod.
Performance and Response of Electric Steering
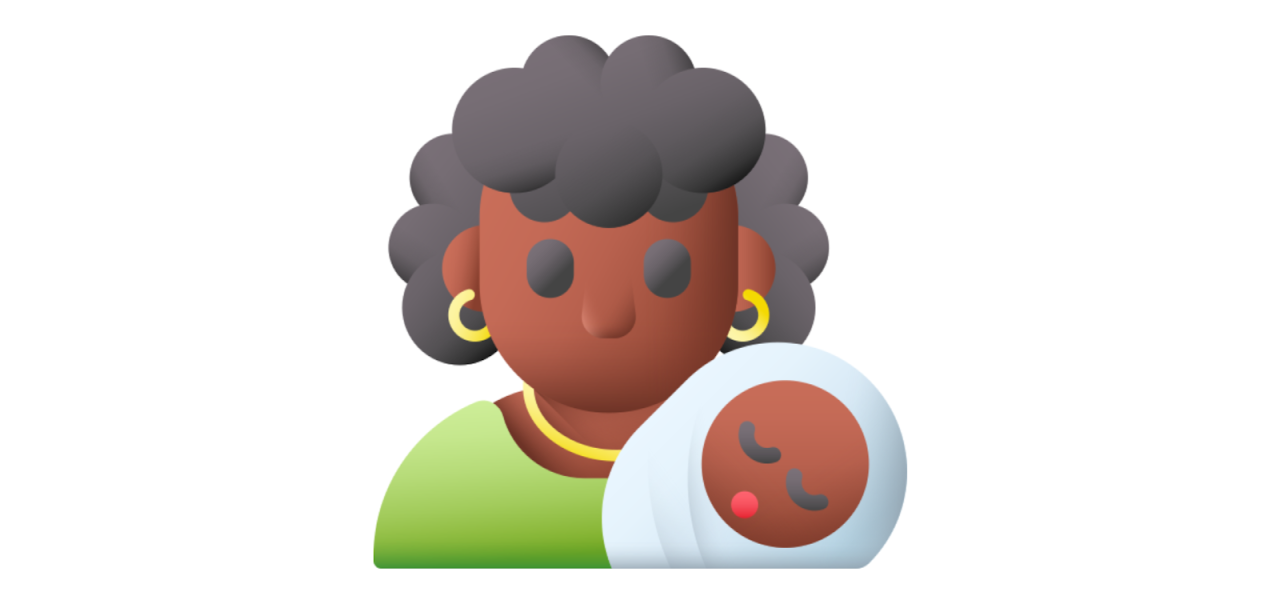
Electric steering systems are rapidly gaining traction in the automotive world, and hot rods are no exception. Their inherent advantages in terms of precision, responsiveness, and customization are particularly attractive to enthusiasts seeking to maximize performance and control in their modified vehicles. This section delves into the specific benefits of electric steering in a hot rod context, comparing its performance to traditional hydraulic systems and analyzing the crucial role of motor selection.Electric steering offers a significant leap forward in terms of performance and control compared to hydraulic systems, particularly in the demanding environment of a hot rod.
The instantaneous response and precise control provided by electric systems are unmatched, allowing for a level of fine-tuning and feel that is nearly impossible to replicate with hydraulics. Furthermore, the ability to customize the steering response allows hot rod builders to tailor the system to the specific vehicle’s dynamics and the driver’s preferences.
Advantages of Electric Steering in Hot Rods
Electric steering’s advantages stem from its inherent characteristics, which translate into superior performance and control in a hot rod application. These include:
- Precise Control: Electric motors provide precise torque output, enabling a very fine level of steering control, especially beneficial in tight turns or demanding driving situations. This precision translates to better handling and reduces the potential for loss of control.
- Instantaneous Response: Unlike hydraulic systems with fluid pressure limitations, electric systems react almost instantly to driver input, reducing steering lag and enabling more immediate and controlled responses to road conditions.
- Customizability: The electronic nature of electric steering systems allows for precise calibration and customization of steering feel, from sensitivity to responsiveness, enabling the hot rod owner to personalize the system to their preferred driving style and vehicle dynamics.
- Reduced Maintenance: Electric systems have fewer moving parts compared to hydraulic systems, leading to less wear and tear, reducing the frequency of maintenance needs and potential repairs.
Steering Feel Comparison
The steering feel of electric steering differs significantly from traditional hydraulic systems. Hydraulic systems often provide a more “bodied” or “heavy” feel, while electric steering can offer a more precise and responsive feel, often described as “lighter” or “sharper.” This difference in feel is critical for the hot rod driver seeking optimal handling and control.
Motor Type Impact
Different motor types affect the steering response and feel. Brushless DC motors are commonly used in electric steering systems due to their high efficiency and precise control capabilities. Their performance often leads to a smoother, more predictable steering feel. Conversely, stepper motors, though often used in other applications, might not be as well suited for the high-torque demands of a hot rod application.
Customization for Hot Rods
Electric steering systems are highly customizable to meet the specific needs of a hot rod. This customization can include:
- Variable Assist Levels: Different assist levels allow drivers to adapt the steering assistance to suit the vehicle’s weight and performance modifications.
- Calibration Options: The steering calibration can be adjusted to tailor the steering feel to the driver’s preference and the specific driving conditions.
- Feedback Mechanisms: Adding feedback mechanisms, such as steering feel simulators, can enhance driver awareness and perception, improving control.
Testing and Calibration Procedures
Thorough testing and calibration are crucial to ensure optimal performance. A comprehensive testing protocol is essential, and this protocol often includes:
- Initial Calibration: The system should be initially calibrated to ensure smooth operation and appropriate response curves.
- Load Testing: Rigorous load testing under various conditions is necessary to evaluate the system’s performance under stress and to ensure the system’s robustness.
- Driver Feedback: Driver feedback and evaluation of the steering feel are essential to ensure the system meets the specific requirements of the hot rod’s dynamic characteristics.
Maintenance and Troubleshooting
Maintaining an electric steering system in a hot rod requires a different approach than traditional hydraulic systems. The components are more intricate, and specific attention to detail is crucial to ensure longevity and performance. Understanding the unique maintenance schedule and potential troubleshooting steps is vital for avoiding costly repairs and maximizing the system’s lifespan.Troubleshooting electric steering systems often involves systematic diagnosis, identifying the root cause of any malfunction.
This proactive approach can prevent minor issues from escalating into major problems. A well-maintained system not only ensures smooth operation but also contributes to the overall reliability and safety of the hot rod.
Specific Maintenance Requirements
Regular inspection and maintenance are paramount for electric steering systems. This includes checking all connections for corrosion and ensuring proper grounding. Visual inspection of wiring harnesses, motor components, and the steering gear are vital. Lubrication schedules should be adhered to strictly, and component wear should be monitored closely. Proper maintenance minimizes the risk of unforeseen failures.
Potential Issues and Troubleshooting Steps
Several potential issues can arise with electric steering systems. Problems may range from minor electrical glitches to more significant mechanical failures. A systematic approach to troubleshooting is key. Isolate the problem by checking for loose connections, faulty wiring, or issues with the motor or steering gear. Consult the manufacturer’s recommendations for specific procedures.
Common Problems and Solutions
- Wiring Issues: Faulty wiring can manifest as intermittent steering operation or complete failure. Troubleshooting involves checking for frayed wires, loose connections, and corrosion. Repairing damaged wires or replacing the entire harness is essential for restoring functionality. Using high-quality connectors and proper insulation techniques is crucial for preventing future problems.
- Motor Malfunction: A malfunctioning motor might result in sluggish or jerky steering response. Inspect the motor for overheating, unusual noises, or visible damage. If the motor is faulty, replacing it is often necessary. Checking for correct voltage and amperage input is also crucial.
- Steering Gear Problems: Sticking or binding in the steering gear can lead to a loss of steering responsiveness. This often indicates worn components within the gear mechanism. Replacing the entire steering gear unit might be required depending on the extent of the damage. Lubrication and proper alignment are crucial for the steering gear to function smoothly.
Replacing Components
Replacing components in an electric steering system requires careful attention to detail. Disassembly should follow the manufacturer’s instructions. Using the correct tools and procedures minimizes the risk of damaging components. Thorough cleaning and inspection of the replacement part is important before installation. Proper reassembly is crucial to ensure the system functions correctly.
Diagnosing and Repairing Common Issues
Diagnosing and repairing issues in electric steering systems involves using a multimeter to check voltage and amperage readings. This helps pinpoint electrical problems. Visual inspection of the system’s components is essential for identifying mechanical issues. Reference the manufacturer’s troubleshooting guide and schematics for specific steps and solutions. Consult a qualified technician if the issue persists or if you lack the necessary expertise.
Safety and Reliability
Electric steering systems, while offering significant advantages in hot rods, demand meticulous attention to safety and reliability. These systems, integrating complex electronics and high-voltage components, introduce unique challenges that must be addressed proactively to ensure the safety and dependability of the vehicle. Robust design, meticulous testing, and adherence to stringent safety protocols are crucial for minimizing risks and maximizing the longevity of the system.Electric steering systems, in contrast to traditional hydraulic systems, offer a different set of potential failure points.
Understanding these points and implementing appropriate safeguards is paramount to maintaining a safe and reliable driving experience. This includes comprehensive testing protocols, redundancy where possible, and robust design features to withstand the rigors of high-performance driving.
Safety Features and Measures
Electric steering systems incorporate various safety features to mitigate risks. These include redundant sensors, fail-safes, and emergency shutdown mechanisms. For instance, redundant sensors monitor critical parameters like voltage and current, providing multiple points of verification for system integrity. Fail-safes automatically engage in case of sensor malfunction or component failure, often reverting to a basic manual steering mode.
Emergency shutdown mechanisms are designed to quickly interrupt power to the system in critical situations, ensuring the driver can regain control of the vehicle.
Reliability Considerations in High-Performance Environments
The reliability of electric steering systems in high-performance hot rods requires careful consideration. High-speed maneuvers, extreme temperatures, and demanding driving conditions can stress the components. Extensive testing, utilizing dynamic simulations and real-world driving scenarios, is critical to ensure the system’s performance under various conditions. Design choices, like using high-quality components with high thermal tolerance, are vital to enhance reliability.
The use of advanced diagnostics, allowing for proactive maintenance, is essential to prevent unexpected failures.
Safety Precautions for Maintenance
Working on electric steering systems necessitates specific safety precautions. High voltage and complex electronics require specialized tools and procedures. Before any maintenance or repair, the system must be properly de-energized and isolated. Qualified technicians, well-versed in electrical safety procedures, should handle these tasks. Appropriate personal protective equipment (PPE), including insulated gloves and safety glasses, should always be worn.
Failure to follow these procedures can lead to serious electrical hazards.
Failure Modes and Impact on Hot Rod Safety
Potential failure modes in electric steering systems can have significant consequences for hot rod safety. Examples include motor failure, sensor malfunction, or component overheating. Motor failure, for example, can lead to loss of steering control, potentially resulting in an accident. Similarly, sensor malfunction could cause erratic steering behavior or the complete failure of the system. Component overheating can cause system malfunctions and potentially lead to fire hazards.
Importance of Regular Maintenance and Safety Checks
Regular maintenance and safety checks are paramount to ensuring the long-term reliability and safety of electric steering systems. This includes periodic inspections of components, checking wiring connections, and verifying the functionality of safety mechanisms. Following the manufacturer’s recommended maintenance schedule is crucial to preventing potential issues. Comprehensive documentation of maintenance activities should be maintained, serving as a record of the system’s health and performance history.
Cost and Accessibility
Electric steering systems for hot rods are poised to disrupt the traditional hydraulic approach, but the financial implications and availability of components are crucial factors for adoption. The initial investment can seem daunting, but potential long-term savings and performance advantages are worth considering. This section delves into the comparative costs, component availability, and factors affecting pricing.Electric steering systems, while offering significant performance benefits, often come with a higher upfront cost than their hydraulic counterparts.
However, the potential for reduced maintenance costs and increased performance can offset this initial investment over time. Furthermore, the availability of components and ease of installation are key considerations for enthusiasts looking to upgrade their hot rods.
Cost Comparison to Hydraulic Systems
Electric steering systems typically have a higher initial cost than comparable hydraulic systems. This difference is often attributed to the more complex nature of the electric motor, control unit, and associated wiring. However, the potential for lower ongoing maintenance costs, especially in terms of fluid changes and potential leaks, can make the long-term cost-effectiveness of electric steering systems more attractive.
Component Availability and Sources
The availability of electric steering components varies depending on the specific system and the vendor. Directly purchasing components from specialized suppliers or companies specializing in electric steering systems for hot rods may be necessary for enthusiasts seeking the highest level of customization and compatibility. Online retailers and aftermarket parts distributors are also potential sources for components, but the availability and quality of components may differ.
Factors Influencing Electric Steering System Cost
Several factors contribute to the overall cost of electric steering systems for hot rods. The complexity of the system, including the motor, control unit, and associated wiring, is a primary determinant. Customizations, such as the inclusion of advanced features or high-performance components, can also increase the overall price. Furthermore, the cost of labor for installation and any specialized modifications required for the specific hot rod model are additional factors.
Pricing Structures for Electric Steering Components
Pricing structures for electric steering components can vary considerably. Some suppliers offer tiered pricing based on the desired performance characteristics and features, while others may provide a fixed price for a complete system. Direct comparison of pricing is important to ensure that the chosen system aligns with budget and performance expectations. For example, a basic electric steering system might cost $3,000-$5,000, while a higher-end system with enhanced features could exceed $8,000.
Purchasing and Installation Steps
The process of purchasing and installing an electric steering system for a hot rod requires careful planning and execution. First, selecting a suitable system that meets the specific requirements of the hot rod is critical. This includes considering the vehicle’s weight, size, and the desired level of performance. Next, obtaining the necessary components and tools is essential.
Lastly, ensuring that the installation is performed by qualified technicians or individuals with experience in such installations is paramount for a successful outcome. Specific installation instructions will be provided by the manufacturer of the selected system.
Electric Steering Integration with Other Systems
Electric steering systems, while offering significant advantages in performance and responsiveness for hot rods, necessitate careful integration with existing mechanical systems. The complex interplay between steering, suspension, and braking demands meticulous planning to avoid detrimental effects on overall vehicle dynamics. Compatibility issues, if not addressed proactively, can lead to reduced performance, compromised safety, and ultimately, an unsatisfactory driving experience.Integrating electric steering with existing hot rod systems presents both challenges and opportunities.
The transition from traditional hydraulic or mechanical systems to electric necessitates careful consideration of power requirements, signal transmission, and control algorithms. Solutions must be robust and adaptable to accommodate the unique characteristics of a hot rod’s performance-oriented design.
Compatibility Issues
Integrating electric steering into a hot rod’s existing chassis can present various compatibility issues. These issues stem from differences in signal transmission protocols, power demands, and physical mounting requirements. For instance, the electrical wiring harness for the electric steering system must be compatible with the existing wiring for other systems, such as lighting, audio, and instrumentation. Furthermore, the electric motor and control unit need to be integrated within the chassis without compromising structural integrity or affecting the aesthetic appeal of the hot rod.
Incompatible mounting points or insufficient space for the new components can also lead to design conflicts.
Integration Strategies
Several strategies can be employed to seamlessly integrate electric steering into existing hot rod systems. One approach involves modifying the existing suspension system to accommodate the new steering components. This might include adjusting the mounting points for the steering rack or incorporating specialized mounting brackets. Another strategy focuses on modifying the braking system to ensure compatibility with the electric steering’s power requirements.
For example, a carefully planned electrical distribution system can ensure sufficient power for both systems without overloading the electrical network. Precisely calibrated control algorithms can ensure that the steering system does not interfere with the braking system’s operation.
Examples of Successful Integrations
Numerous hot rod enthusiasts have successfully integrated electric steering systems into their builds. These examples demonstrate the potential for enhancing performance and driving experience. For instance, some builds have incorporated electric steering systems into vehicles with custom suspension designs, demonstrating the feasibility of integrating advanced systems into existing chassis. Other successful integrations have involved carefully modifying existing braking systems to maintain optimal braking performance during high-speed maneuvers, emphasizing the importance of comprehensive testing and calibration in these complex projects.
Detailed documentation and shared knowledge within the hot rod community have contributed to these successful implementations.
Benefits of Integrated Systems
Integrating electric steering with other systems, such as suspension and braking, offers several key benefits. These benefits include enhanced responsiveness and control, allowing for precise steering inputs even under demanding conditions. Furthermore, optimized power distribution and signal transmission can lead to improved safety and reliability. A well-integrated system also potentially leads to a more balanced and refined driving experience, aligning the vehicle’s performance with the desired handling characteristics of the hot rod.
Future Trends and Innovations
The electric steering market is poised for rapid evolution, driven by advancements in battery technology, motor design, and control systems. This evolution promises significant implications for the performance and appeal of electric steering systems, particularly in niche applications like hot rods, where customization and unique performance characteristics are highly valued. The future will likely see a convergence of high-performance demands with sophisticated control algorithms.Electric steering systems are not just about replacing hydraulics; they are about reimagining the driving experience.
This includes enhancing responsiveness, precision, and overall feel. These advancements, coupled with evolving consumer preferences, will shape the trajectory of electric steering, particularly within the hot rod community.
Emerging Trends in Electric Steering Technology
Electric steering systems are progressing beyond basic replacements for hydraulic counterparts. The latest advancements incorporate sophisticated control algorithms, allowing for more intuitive and personalized driving experiences. This includes dynamic adjustments based on road conditions, driver input, and even vehicle speed.
Potential Future Innovations in Electric Steering Systems
Several key innovations are likely to emerge in the coming years. One area of significant potential is the development of active steering systems that adapt to the road surface in real time. This could improve handling and safety, especially on uneven or challenging terrain. Furthermore, integrating predictive modeling into the control algorithms will allow the system to anticipate driver inputs, enhancing responsiveness and feel.
Potential Impact on Steering Performance and Feel
The integration of advanced sensors and algorithms will likely lead to a more nuanced and refined driving experience. The responsiveness and precision of electric steering will be enhanced, providing drivers with a more direct and connected feeling to the road. This increased responsiveness and feel is particularly important for the hot rod enthusiast who values direct steering feedback and dynamic handling.
Advanced Electric Steering Systems and Their Characteristics
Examples of advanced electric steering systems include those incorporating adaptive damping, where the system adjusts the steering response based on real-time road conditions. Systems employing predictive modeling could anticipate driver actions, enabling more responsive steering and reducing lag. These systems often utilize high-performance motors, sophisticated control algorithms, and advanced sensors for accurate feedback and precise control.
Predictions for the Future Development of Electric Steering
The adoption of electric steering in hot rods will likely accelerate as the technology matures and costs decrease. Expect more readily available components and kits tailored for specific hot rod builds. Integration with other electric vehicle technologies, like regenerative braking, could also become more prevalent, further enhancing the overall performance and efficiency of the system. This is consistent with the broader trend of electric vehicle adoption and the desire for customizable performance characteristics in the hot rod community.
Real-World Examples
Electric steering in hot rods is no longer a futuristic concept; real-world implementations are demonstrating the technology’s viability and potential. These projects offer valuable insights into the challenges and rewards of integrating electric powertrains into classic American automotive designs.
Early Adopters and Customization
Early adopters of electric steering systems in hot rods often prioritize customization and performance enhancement. Modifications range from complete replacement of the traditional hydraulic steering system to hybrid setups where electric assist supplements the existing hydraulic system. These bespoke solutions showcase the adaptability of electric steering technology to diverse vehicle configurations.
Modifications and Adaptations
Numerous modifications are necessary for the successful integration of electric steering. These often involve redesigning the steering column, replacing the steering gear, and installing the electric motor and associated control systems. Careful attention to maintaining the aesthetics of the hot rod while accommodating the new components is crucial. For example, some builders might incorporate custom fabricated brackets and housings to integrate the electric motor discreetly within the chassis.
Performance and Response Data
Performance data, while not always readily available publicly, often demonstrates improved response times and reduced effort in turning compared to hydraulic systems. This can lead to a more precise and enjoyable driving experience. However, some early projects may have experienced issues with calibration and control responsiveness, requiring adjustments and refinements.
Challenges and Successes
One significant challenge is the need for a dedicated battery system to power the electric motor. This necessitates careful consideration of the battery placement, sizing, and capacity to ensure optimal performance and range. Successes often stem from meticulous planning and meticulous implementation. Some projects have successfully integrated the electric steering system with other electric components, such as electric brakes or power windows, creating a fully electric powertrain.
Integration Examples
One example is a 1932 Ford roadster, where the entire steering system, including the steering column, steering gear, and power unit, has been replaced. The electric motor was positioned within the chassis, concealed by custom fabricated components, maintaining the car’s original aesthetics. This project aimed to enhance responsiveness and improve overall driving dynamics, though specific performance metrics were not readily available.
Another example is a 1957 Chevrolet Bel Air, where a hybrid approach was adopted. The existing hydraulic system was retained, but an electric motor was integrated to provide variable assist depending on steering inputs, increasing maneuverability in tight spaces.
Conclusion
Real-world examples of electric steering in hot rods are emerging, showcasing the versatility and potential of this technology. While challenges remain, the integration of these systems offers a promising avenue for enhancing the performance, customization, and sustainability of classic American vehicles. The continuous development of electric steering technology, coupled with innovative design solutions, will likely lead to even more impressive real-world implementations in the future.
Aesthetic Considerations
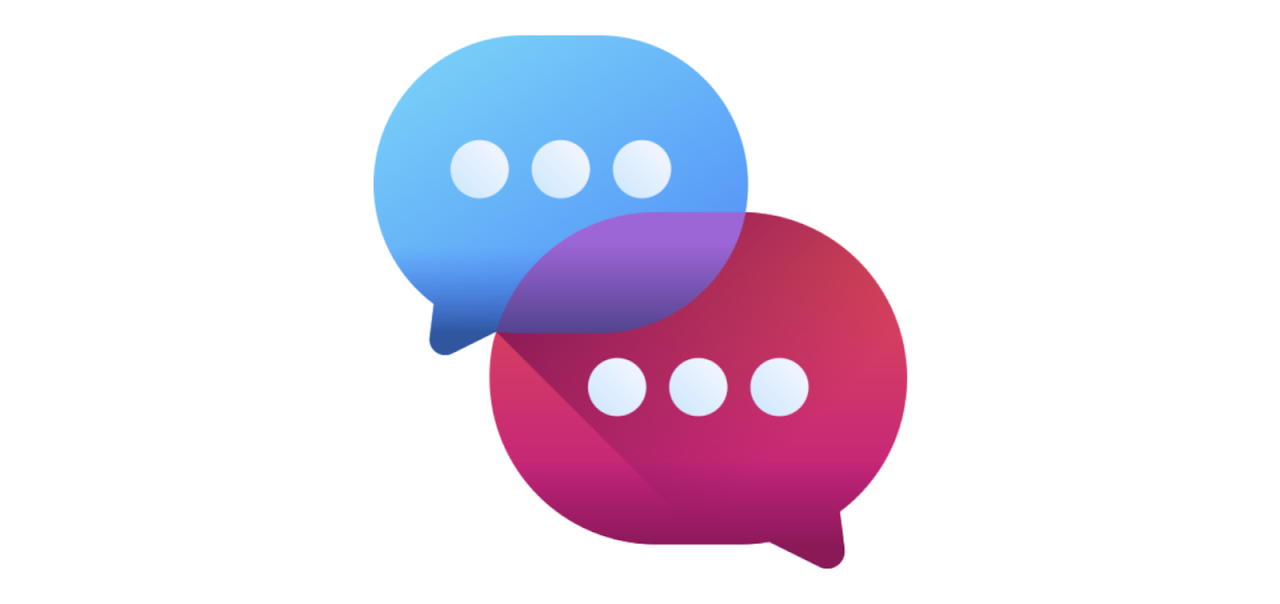
Electrifying a hot rod isn’t just about performance; it’s about creating a unique visual statement. The aesthetic integration of electric steering components is crucial for achieving a cohesive and visually compelling design, reflecting the modern, high-performance nature of the vehicle. This section explores the strategic incorporation of these components into the overall aesthetic.
Integrating Electric Steering into the Hot Rod’s Design
The design philosophy for electric steering in a hot rod should prioritize clean lines and a streamlined appearance. Avoid cluttering the vehicle with oversized or visually jarring components. Instead, integrate the system into the car’s existing design language. Concealing components within the vehicle’s structure or using materials that complement the hot rod’s style are key considerations. This requires a thorough understanding of the components’ physical dimensions and their potential impact on the overall aesthetic.
Concealing Components
Aesthetically pleasing integration often involves concealing the components. This can be achieved through clever design choices, such as embedding the motor housing within the frame or using custom-fabricated shrouds to blend the electric steering components with the car’s body. Precise design calculations are crucial to ensure proper function without compromising the aesthetic appeal. For instance, a seamless integration of the motor housing within the front suspension would create a clean, modern look.
Material Selection for Components
The choice of materials for casing the electric steering components plays a significant role in the final aesthetic. Lightweight, high-strength aluminum alloys, or even carbon fiber, can create a modern, sporty look. These materials can be further enhanced with polished finishes, or textured surfaces, to create a more refined and unique aesthetic. For a more classic hot rod style, polished stainless steel or brushed aluminum could be suitable.
Consider the overall colour scheme and existing paintwork of the vehicle when selecting the material for the casing.
Examples of Aesthetically Pleasing Designs
- Sleek and Modern: A minimalist design with concealed components, employing high-gloss black or deep-red painted aluminum housings for the electric motor and steering unit. This aesthetic is best suited for a hot rod with a modern design language.
- Classic with a Twist: Using polished stainless steel components with a brushed finish to complement a traditional hot rod aesthetic. This method seamlessly blends the modern technology with the classic look. The detailing could be enhanced with subtle chrome accents.
- Custom-Designed Shrouds: Creating custom shrouds for the components in a bold color or with intricate patterns. This allows for a unique and visually striking appearance, which would be ideal for a hot rod with a bespoke style.
Design Style Comparison
Design Style | Aesthetic Appeal | Material Suggestions |
---|---|---|
Sleek and Modern | Clean lines, minimalist approach | High-gloss black aluminum, carbon fiber |
Classic with a Twist | Blends modern technology with traditional aesthetics | Polished stainless steel, brushed aluminum |
Custom-Designed Shrouds | Bold and unique appearance | Painted aluminum, carbon fiber, stainless steel |
Concluding Remarks
Electric steering for hot rods represents a fascinating convergence of cutting-edge technology and classic automotive passion. This technology promises a future where precise control, customizable feel, and potentially even reduced maintenance are hallmarks of hot rod performance. The detailed analysis of components, design considerations, performance characteristics, and integration with other systems provides a comprehensive guide to navigating this exciting new landscape.
Ultimately, this exploration highlights the transformative potential of electric steering in reshaping the future of hot rod engineering.